Case Studies
Howdon delivers the right results for new electric vehicle testing rig
Howdon Torque Limiters have been involved in the design and manufacture of torque limiter couplings for over 40 years and, in recent times, has worked with other engineering companies on developing test rigs for the automotive industry.
Paul Reid, Project Manager at Zytek Automotive Ltd, Continental Engineering Services, explains: ”We had been developing a test rig for two years to help a client test a manual clutch system for new Hybrid and Electric vehicles. The problem was that we needed a torque limiter coupling that could run up to speeds of 6500 rpm and 900 Nm, but be small enough to fit into our newly designed test rig.
Howdon Wedgegard torque limiters gave us the following advantages over standard slip clutches:
First and foremost, Safety. Torque limiting couplings play a large role in test rig safety as they protect the shafts from breakages due to lock-up conditions. If a rig were to lock without them, it would most likely result in a shaft breakage, which would could eject significant fragments to cause injury, even when guarded. Fitting the Howdon WedgeGard coupling significantly reduced the effort to design the guards and test them, as the ejected fragment size (and energy) is vastly reduced.
Direct mating to an HBM-T40B torque flange for protection of expensive sensors.
The limiter coupling also had to mate directly to an HBM T40B torque flange, an expensive torque sensor widely used in the automotive industry. The torque flange usually has a 100% overload around 1000 Nm so the WedgeGard must break before 2000 Nm.
Reliability – no moving parts.
Having looked around in the market, Howdon seemed to have the expertise to create a bespoke torque limiter that would work for our application. Unlike other solutions we’d tried and products we’ve used in the past, Howdon’s DIN 120 coupling didn’t need any balancing and worked first time.
Relatively easy to achieve alignment of 30 microns.
We could achieve <30 microns with just a screwdriver forced in the gap between the two flanges, then lock the bolts on the wedgepins to hold the alignment. There was significant lash in the bearings without the wedgepins at well over 30 microns which could cause a vibration.
Promotes inspection in the testing process.
When a pin breaks a technician must fit a new one. This automatically promotes an inspection, as the guy needs to have hands on the rig, whereas a slipper clutch will recover and nobody will ever look at why it slipped. So if the rig bearings were deteriorating and causing excessive torque (friction, etc), this would be found by changing the pins.
This was a quick turnaround job and their customer service was excellent, answering all our technical queries straight away.“
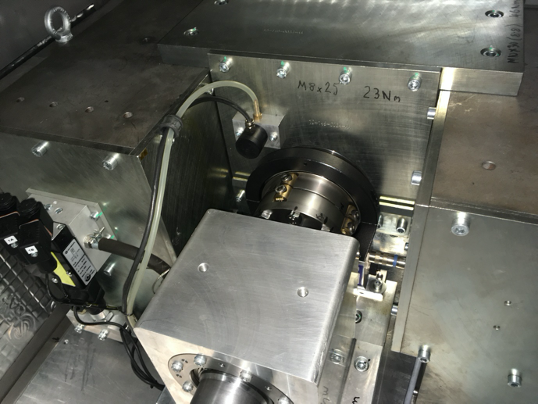
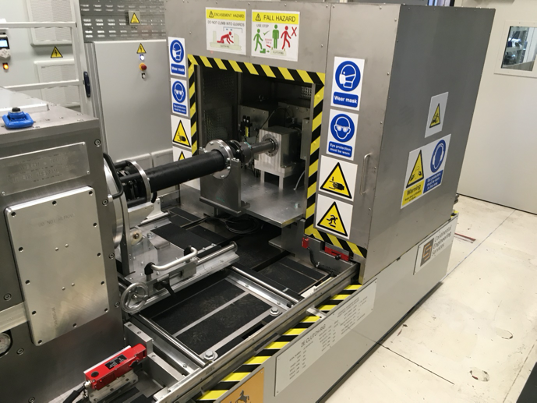
Wedgegard DIN-120 shear couplings fitted to the 2E test rig
Howard Miles, MD of Howdon, commented: “Our products have always been designed to the highest standard and we guarantee that the limiters will disengage at the required breaking load within 3% of accuracy. Unlike slip and ball clutches which can degrade over time, our mechanical solution continues to break at the same point for year after year, meaning a guaranteed level manufacturing success and quality control in car part production. Our torque limiters have also found their way into full test beds of whole vehicles as well, allowing manufactures to test everything from motors and breaking systems to clutches.”
Howard added: “It’s great to collaborate with other engineering businesses in the UK to help support EV manufacturing around the world. We’re proud to be part of the automotive industry and Made In Britain.”
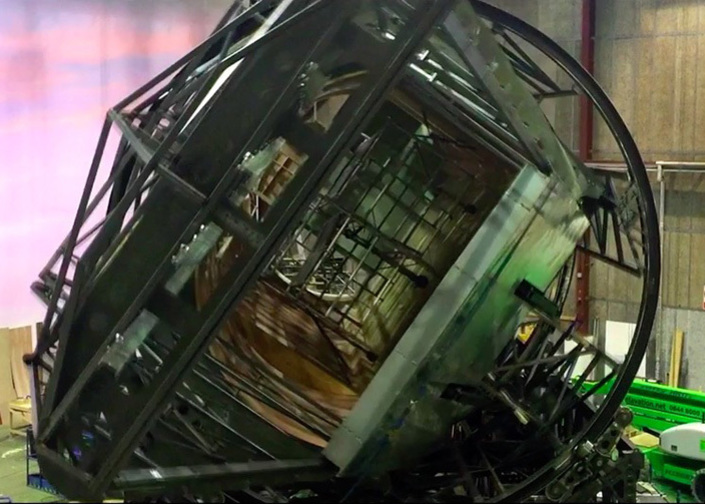
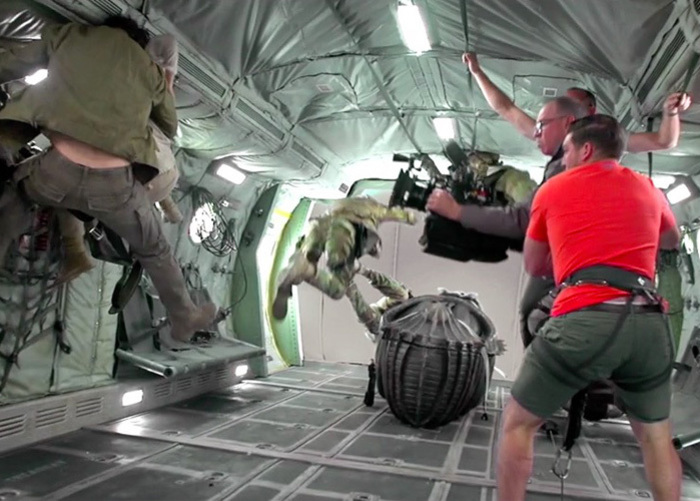
Images of giant film set with spinning gimbal built to look like the inside of a C-130 plane
British engineering company Howdon puts the brakes on Hollywood!
Howdon Power Transmission of Stroud has been supplying torque limiters and industrial brakes since 1977. In that time they have been asked to provide help to solve many movement issues on large pieces of machinery, from overload protection to braking on massive spinning wheels.
Howdon products are used in all sorts of applications, from car production to agriculture and even Hollywood blockbuster film sets.
“Over the years we get these types of odd enquiries from various film companies around the world. Sometimes we know the movies our kit will be used in and other times it’s all top secret”, explained Howard Miles, the MD of Howdon.
“Just like on the 2017 movie ‘The Mummy’ – at the time we didn’t know that our industrial brakes would be used to slow down a massive spinning aeroplane set with Tom Cruise inside. And I’m glad to say our brake performed beautifully and we didn’t kill him.”
Erik Nash, Production & Visual Effects Supervisor on ‘The Mummy’ said: “The gimbal was a pretty spectacular piece of engineering itself. It was basically the entire cargo hold of a C-130, built to be able to rotate and roll 360 degrees continuously. I think they could do up to nine consecutive revolutions at up to five seconds per revolution and the reason they couldn’t go continuously is that all the cabling to power the lights and everything else inside the set would get wound up.”
Howard Miles added “It just goes to show that a career in engineering can lead anywhere and into many different problems to solve. At present our products are being used in another blockbuster, due for release next year but we can’t say which one!”
Images copyright ©Universal Pictures and © 2019 Visual Effects Society.
XYZ machine tools bring flexibility to Howdon Power Transmission’s product development
Founded over 40 years ago Stroud-based Howdon Power Transmission is the originator of the patented Wedge Pin system for mechanical overload protection. Patented back in 1978 the Wedge Pin remains central to the company’s range of Wedgegard Torque Limiters. With such a well-established product it could be expected that development was minimal, but that is far from the case, with new applications arising on a regular basis product updates are a common occurrence, and time-to-market is crucial.
With such a varied product range and a worldwide customer base, with significant sales in the USA, Africa, mainland Europe and of course the UK, demand for Howdon Power Transmission’s Wedgegard Torque Limiter products continues to grow, along with the need to innovate the Wedge Pin.
The Wedge Pins are effectively ‘mechanical fuses’, which are designed as a weak link when a certain torque is reached, thereby preventing serious damage to rotary power transmission systems.
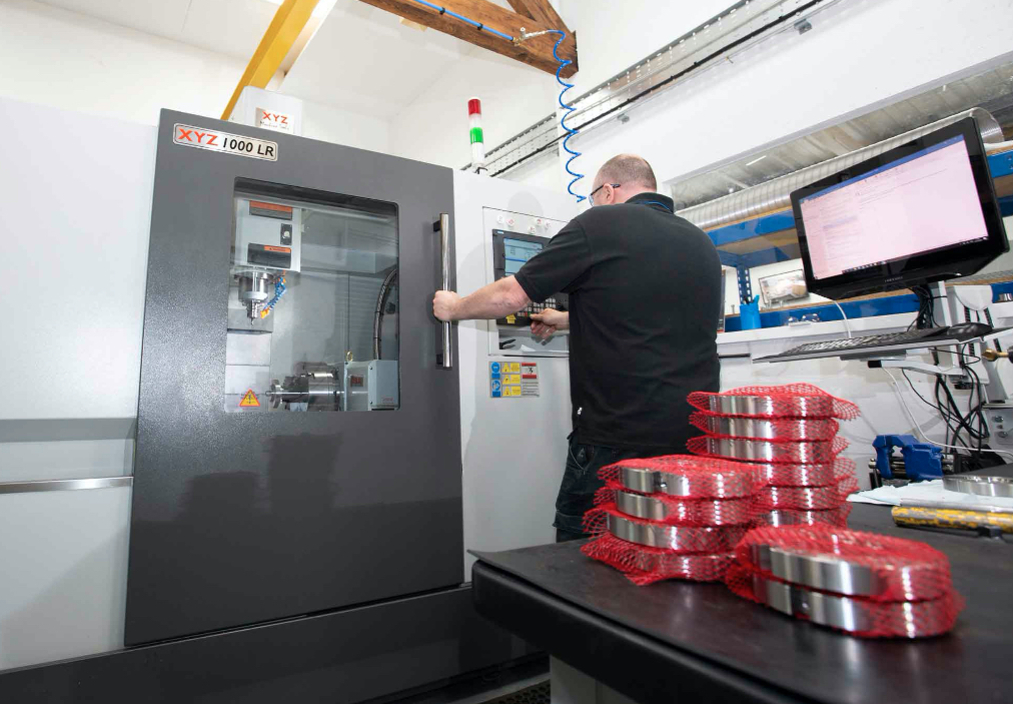
While standard production of these parts is given over to long-term sub-contract partners, Howdon Power Transmission needed greater flexibility and versatility when it came to machining for research and development; as well as low volume production to meet urgent demand from customers design for bespoke applications. “Our products cover such a wide range of applications from steel mills through food production to on-vehicle installations, therefore we are constantly looking to develop the design and, while sub-contract manufacture for production is ideal for us, we needed faster reactions when it came to product development and testing,” says company founder and managing director Howard Miles.
The search for suitable machine tools took Howdon Power Transmission far and wide, but eventually led to XYZ Machine Tools, just down the M5 motorway, where it had a demo of an XYZ SLX 1630 ProTURN lathe. Howdon Power Transmission’s works manager Neil Hussey was won over by the ProtoTRAK control and its ease of use, which lends itself to the one-off and low volume machining that he had in mind. He says: “The ProtoTRAK control is ideal for our needs. I can quickly generate programs from initial sketches at the machine and the TRAKing and Verify capability of the control give the confidence that the first off will be correct, without any fear of collisions when the cycle start button is pressed.” With turning capacity taken care of attention switched to machining centre capability and given the size and type of work undertaken the choice of machine was an XYZ 1000 LR vertical machining centre. This machine is part of the XYZ LR series which makes use of linear rail technology for axis travel, this provides a lower cost introduction to machining centre ownership, however, price was not a major consideration for Howdon Power Transmission. “Performance and specification were our main priorities when choosing a machining centre,” says Howard Miles. “We then wanted the security of local support and training, which we get from XYZ Machine Tools. Neil had one day of training down at XYZ in Burlescombe and we still have two days of free training left, which we will undertake on-site here when we need it, but so far we are managing to achieve everything we want with the machines and knowledge that we have.”
Backing up Howdon Power Transmissions decision to go for specification and performance is the standard build of the XYZ 1000 LR, which comes with an 18 HP/13kW 8000 revs/min spindle with axis travels of 1000 by 500 by 500 mm (xyz) and a table size of 1060 by 500 mm. also specified as an option was a 4th axis unit to add greater versatility and productivity. One key feature was the 24 position arm-type tool magazine as Neil Hussey explains: “It seemed like a sensible option to specify, we have a machining centre that is quick to program and set-up, so to be constantly changing tools would be time consuming, so to keep the magazine full, with a variety of tools makes changeovers even quicker.”
Chris Issac of design and marketing specialists Isaac & Isaac commented: “As a member of the Made in Britain organisation, Howdon Power Transmissions is rightly proud of the fact that what this ‘local’ engineering company in Stroud produces goes to customers around the world. Their brand is well-known thanks to its longevity, but they are aware that they need to keep innovating and developing new products. Having this in-house machining capability enhances their ability to do that by shortening the time to market for new ideas and bespoke offerings for customers.”